This section is probably the most indigestible part of the presentation. I invite therefore all those who do not like technology or are even repulsed by it, to quickly move to the next topic.
I will discuss here briefly the technique to manufacture wooden clocks in its three main topics:
The first topic concerns the choice of materials

I use birch plywood of aircraft quality for gearwheels and of cherry or boxwood for small pinions. The teeth of wheels and pinions are used as-machined. Only edges need to be deburred. The axes are in beech wood or brass tube and rotate in micro bearings which I realize in PTFE (Teflon). The hands are made of walnut wood. The frame is of walnut, bamboo, elm, cherry or exotic wood depending on the model and the desired veining or colour. Appearance and dimensional stability are the main criteria for selection of these types of wood.
The second topic relates to design

All models (including the first two for which I bought the drawings) are computer designed and processed, including calculation and plotting of pinion teeth with associated spacings. As I do not replicate clock models that existed in past centuries, I am not forced to reproduce tooth profiles known and used during these periods. I opted for the “involute” tooth profile because it is rather insensitive to dimensional changes of the wood, which are due to humidity absorption which depends on local climatic conditions. I also know well its definition. However, the small gears that have 8-15 teeth must have profile teeth with an offset for better meshing. I also recalculated the kinematics of different escape systems which, in cooperation with the balance wheel, limit and stabilize the rotation of the gears and hands they turn.
The third topic covers the crafting of clocks
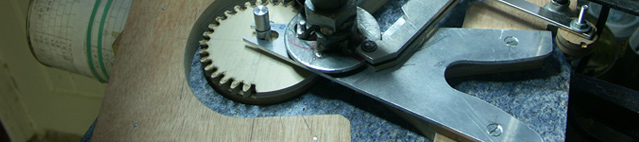
Each model is unique. I could have opted for the use of a numerically controlled 3 to 5 axe machine but this –up to me- would only make sense for mass production of clocks. I therefore started creating and producing all my own tools that allow me to always have the same level of precision of better than 1/10th of a millimetre. Of course, progress is slower! But the result is appreciable and I keep complete control of the global system manufacturing process.
My main tools are the planer, router, band saw, scroll saw, a rotary sander, and now also the metal lathe-mill and a divider tray, all of them miniature.
In addition the homemade tools: sensitive drill, double disc sander; the pantograph, fitted with a “Dremel” screwed between two nuts welded together seen above, are totally homemade. Have a look at the tin can at the left for graduation of the divider tray (the 2 rubber bands are moved to change the number of teeth), the purple plate is a scrap of kitchen top. Well, I just finished refurbishing it all a little better.
Tuning, very time-consuming in the beginning, now only takes little time. Experience allows to better differentiate between the apparent and real causes of problems. However, since all models I realize are very different from one another, there still always are a few surprises that, if they do no stop time, do stop progress. They do not prevent me from sleeping at night even if wood still “works” when I sleep!
I always look for the minimal weight size to make the clock operate. Currently, a 500 gram weights descending 1 meter is enough for 1 day of operation. Therefore weights between 550 and 650 grams are selected depending of the escape principle.
A drift of 1 to 3 minutes per day is usual and acceptable to me. Each new pendulum model is designed to receive an optional quartz clock which guarantees time keeping even when the mechanical clock stops when the weights reach their lower position. The “clé de sol” model features this item. And my goodness, I do not regret this feature especially when I forget to raise the weights.
I abandoned the idea of automatic rewinding of the weights.