Cette rubrique est sans doute la partie la plus indigeste de la présentation. J’invite donc tous ceux qui n’y sont pas sensibles ou que cela rebute profondément de vite passer à la rubrique suivante. J’aborde ici succintement la technique utilisée pour la fabrication des horloges en bois sous ses trois sujets principaux.
Premier sujet :
Le choix des matériaux

J’utilise du contreplaqué de bouleau de qualité aviation pour les roues dentées, du merisier ou du buis pour les petits pignons. Les dents des roues et pignons sont « brutes d’usinage ». Seules les arêtes doivent être ébavurées. Les axes sont en hêtre ou en tube de laiton et tournent dans des micro-paliers que j’usine dans du PTFE. Les aiguilles sont en noyer. Le bâti est en noyer, bambou, orme, merisier ou en bois exotique suivant les modèles et les choix du veinage ou de la couleur recherchée. L‘os et la corne de bovidés ont fait aussi leur entrée. L’aspect et la stabilité dimensionnelle sont les critères principaux pour le choix de ces essences de bois.
Second sujet :
La conception

Tous les modèles (y compris les deux premiers pour lesquels j’ai acheté les esquisses) sont créés et travaillés sur ordinateur, y compris le calcul et le tracé des dents des pignons avec les entraxes associés. Ne reproduisant pas des modèles d’horloge ayant existé au XVIIIème siècle, je ne suis pas contraint de reconduire les profils des dentures connus et utilisés à cette époque.
J’ai opté pour le profil de ces dents celui de la « denture à développante de cercle » car il est peu sensible aux variations dimensionnelles du bois inhérentes à l’absorption d’humidité qui est fonction des conditions climatiques du lieu. J’en connais également bien la définition. Les petits pignons qui ont de 8 à 15 dents doivent cependant avoir une denture dite « déportée » pour permettre un bon engrainement. J’ai aussi recalculé la cinématique des différents systèmes d’échappement qui associés au balancier limitent et rendent constant la rotation des pignons et des aiguilles qu’ils font tourner.
Troisième sujet :
La fabrication artisanale des horloges
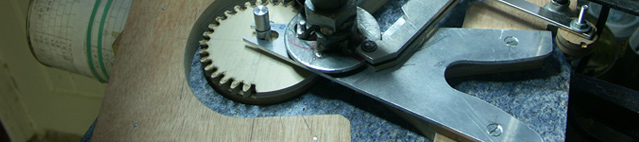
Chaque modèle est unique. J’aurais pu opter pour l’utilisation d’une machine à commande numérique de 3 à 5 axes mais ce qui pour moi n’aurait de sens que pour la production en série des horloges. J’ai donc commencé par créer et fabriquer tous mes outillages qui me permettent de toujours avoir le même niveau de précision inférieur au 1/10ème de mm. Bien sûr, cela va moins vite ! Mais le résultat est à la hauteur et je garde l’impression de m’approprier la fabrication totale du système.
Mes principaux outils sont la raboteuse, la défonceuse, la scie à ruban, la scie à chantourner, une ponceuse rotative, et maintenant le tour-fraiseuse à métal et un plateau diviseur, le tout en petits modèles.
Puis les outillages faits maison: la perceuse sensitive ; la ponceuse à double disques ; le pantographe équipé de la « Dremel » vissée dans deux écrous soudés entre eux, visibles ci-dessus est totalement faits maison ; voyez la boite de conserve à gauche pour les divisions du plateau diviseur (on déplace les deux élastiques verts pour changer le nombre de dents), le plateau violet qui est une chute de paillasse de cuisine. Bon, je viens de refaite tout ça un peu mieux.
La mise au point bien longue au départ me prend aujourd’hui assez peu de temps. Avec l’expérience, je fais mieux la différence entre les causes apparentes de non fonctionnement et les causes réelles. Mais comme les modèles que je fabrique sont tous fortement différents, j’ai quand même toujours quelques surprises qui sans arrêter le temps arrêtent bien le mouvement. J’en dors quand même la nuit bien que le bois travaille toujours, lui !
Je recherche toujours le poids mini qu’il faut pour faire tourner l’horloge. Maintenant, un poids de 500grammes descendant de 1 mètre suffit à les faire fonctionner pendant 1 jour. Puis je choisis entre 550 et 650 grammes suivant les principes d’échappement utilisés.
Une dérive de 1 à 3 minutes par jour est courante et me satisfait. Chaque nouveau modèle à balancier est conçu pour pouvoir recevoir en option un mouvement à quartz de type pendulette qui garantit la tenue de l’heure, même lorsque le mouvement mécanique est arrêté lorsque le poids est en bout de course. Le modèle « clé de sol » en est équipé. Et ma fois, ça ne me déplait pas surtout lorsque j’oublie de remonter le poids.
Sur certains modèles, le poids est remplacé par un système placé latéralement et réarmé toutes les 7 ou 8 minutes par un mini moto-réducteur et quelques composants électroniques. Le tout est alimenté par une petite pile 9V qui assure un fonctionnement annuel.